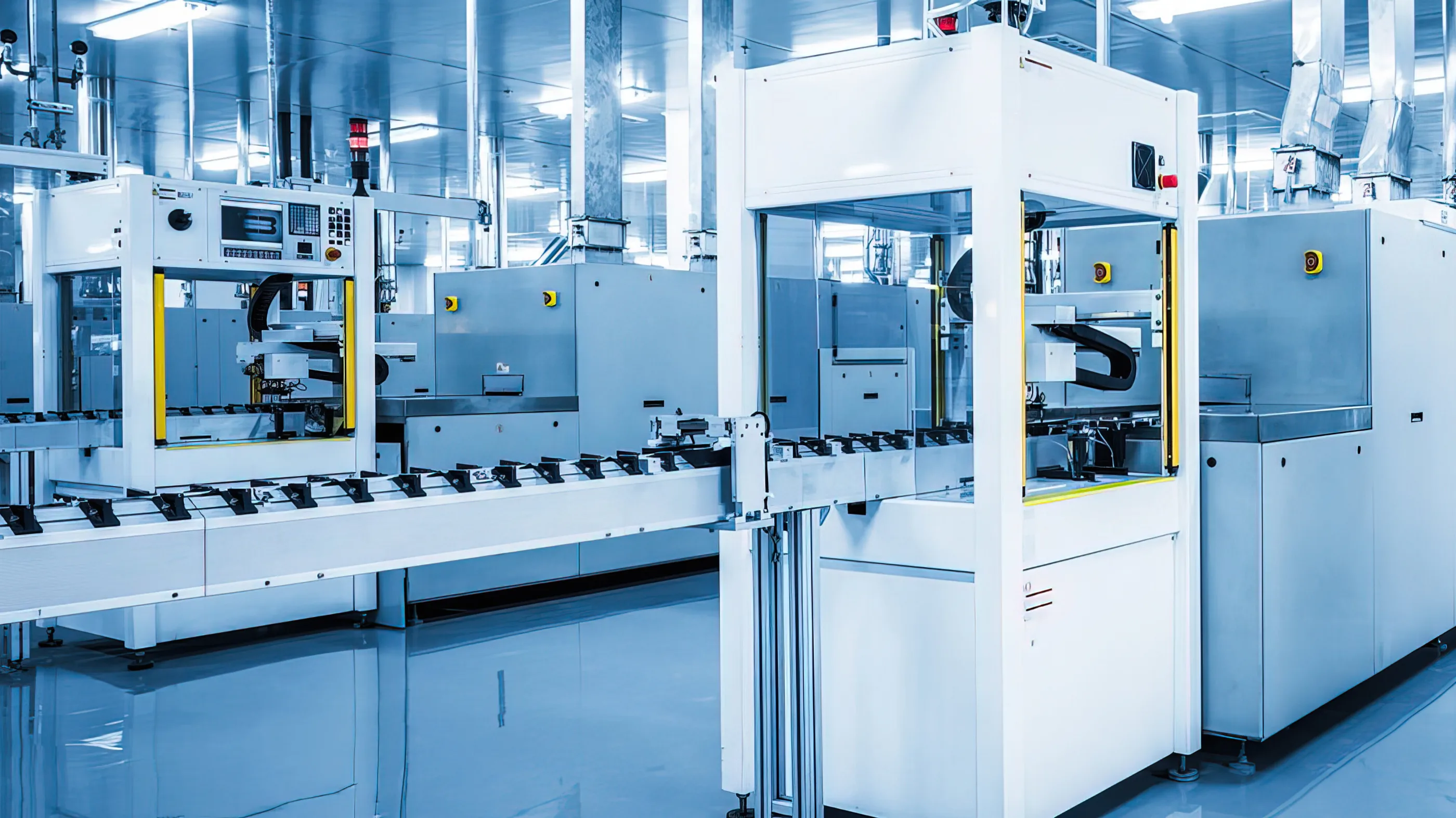
Working with Electronics Manufacturing Service organisations
A common question our customers ask us during the planning of a new product development project is how and when we should engage with the Electronics Manufacturing Service (EMS). Quite rightly they want to know as early in the development cycle as possible how much their new product will cost to manufacture: if a product can’t be made for the right price, it won’t be made at all.
Our experience is that the design team and the EMS should work closely together throughout the development programme, but that the degree of engagement will vary depending on the project stage. Technical design challenges at the proof of principle stage will be solved more quickly if considered independently of finer manufacturability details, but as the design matures, the voice of the EMS becomes increasingly more important to avoid the risk of large scale design changes at a late stage in the project.
Engaging the manufacturing partner early in the process allows preliminary conversations around the general manufacturing and testing approach, and identification of design rules and design constraints which can steer the design in the right direction. Early EMS input on costs helps with the selection of key components. Two components from the same supplier may be obtained together at a lower cost than the sum of other individually cheaper components, or production volumes may have unexpected effects on pricing. While a CR2032 battery is larger and has more capacity than other smaller lithium coin cells, it is produced in greater volume and therefore is often available at a more advantageous price.
It is then tempting to use the EMS to make all of the prototype PCBAs as the design matures. Although this builds the working relationship and can highlight manufacturing issues early, we don’t encourage it. Our experience is that EMS processes designed to drive down volume cost can significantly slow down early prototype development. The time taken to obtain components from approved suppliers on full reels, or process Valor reports to tweak footprints and solder mask details can be longer than the entire PCBA procurement process from a low-volume prototype supplier. Of course, the cost per board from a low-volume supplier will be higher than from the volume EMS, but the focus in the early stages is on quickly obtaining small numbers of PCBAs for testing and debugging of the design before the next iteration.
As the design matures and becomes more stable, conversations start with the EMS around testing both the PCBA and the assembled product. In PCBAs for modern compact products, space for test points is at a premium and a test point per node to allow for in-circuit test is generally no longer possible without adversely affecting the overall product size. We consult with the manufacturer to agree on the test requirements during assembly, usually based on the process FMEA, and then look at which nodes require test points, when these test points must be accessible as the product is assembled and where they can be placed. It is often possible to use a PCBA’s microcontroller to exercise circuit outputs, read signals and communicate with a tester in place of test points, probes and external test equipment.
Following initial prototyping, the design becomes ready for first pre-production prototype manufacture and assembly by the EMS. This is the appropriate time for a more detailed DfM loop, iterating the PCBA design to increase yield before the EMS manufactures boards. Our preferred approach is then for the EMS to firstly supply us with individual untested PCBAs, and other device components that they are supplying. We inspect and test the boards, then perform a first product assembly and resolve any design issues that arise. We also aim to manually run the PCBA and product manufacturing tests on these first units, to establish whether there are any issues with the test approach.
Following any modifications from first pre-production assembly and once we have a small number of working pre-production prototypes that have been assembled and tested at DCA, we can visit the EMS and work with them to troubleshoot the assembly and test process at their premises. This separates the task of establishing that the prototype can be assembled and tested from implementing this on the volume production line, avoiding the potential need to solve problems in both these areas at once.
In summary, we aim to work with our customers’ selected EMS partners throughout the design and development process, but engaging them at an appropriate level every step of the way. Our aim is gaining their inputs to ensure that even our early proposals are practical, producible and testable, but equally to avoid spending lots of time and effort tweaking early concepts for volume manufacture when design changes are still likely. Such premature Design for Manufacture activities will slow down the development process and any effort in this area will most likely need to be repeated until the design solution has stabilised.
Written by Aidan O’Hare, Electronics Skill Leader